From Automotive to Aerospace: Applications and Innovations of PA66 GF33
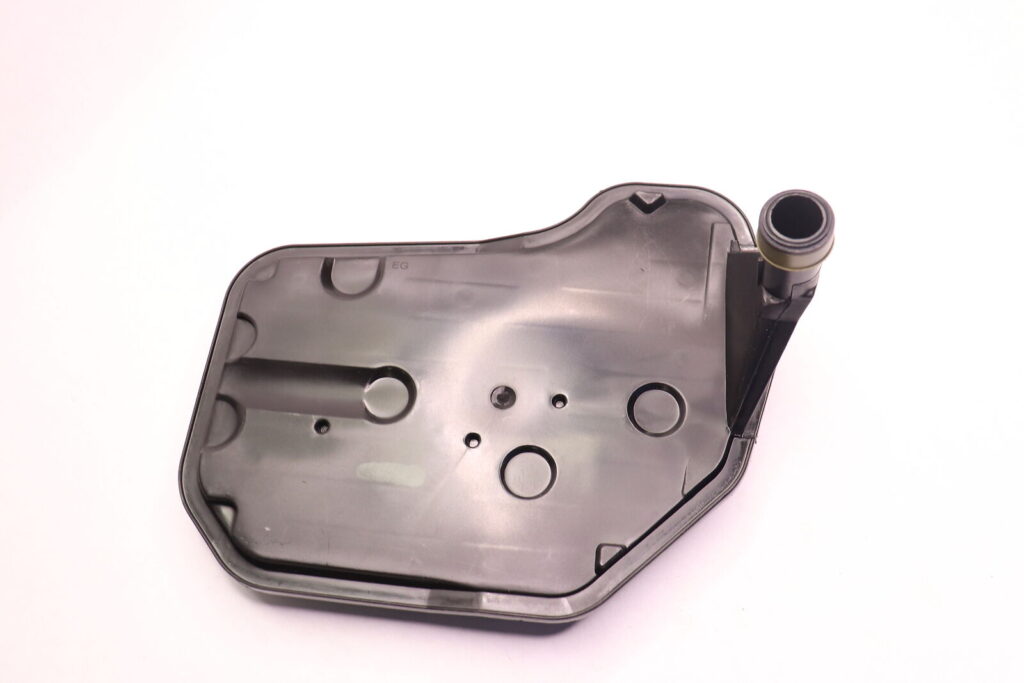
In recent years, the demand for high-performance materials in various industries has surged, driven by the need for lighter, stronger, and more durable products. One such material that has gained significant attention is PA66 GF33, a type of polyamide reinforced with 33% glass fiber. Originally used extensively in the automotive sector for its excellent mechanical properties and heat resistance, PA66 GF33 is now making waves in the aerospace industry due to its exceptional performance characteristics. This article explores the wide range of applications and innovative uses of PA66 GF33 in both automotive and aerospace sectors, highlighting its unique features that make it an ideal choice for these demanding environments.
Overview of PA66 GF33 and its properties
PA66 GF33, or polyamide 66 reinforced with 33% glass fiber, is a high-performance material that finds extensive applications in the automotive and aerospace industries. The inclusion of glass fibers greatly enhances the mechanical properties of PA66, making it stronger and stiffer than its unfilled counterpart. This material also exhibits excellent resistance to heat, chemicals, and abrasion, making it ideal for demanding environments.
In the automotive sector, PA66 GF33 is widely used in various components such as engine covers, intake manifolds, air ducts, fuel lines, and radiator end tanks. Its superior strength-to-weight ratio makes it an attractive choice for lightweighting initiatives without compromising on performance or safety. In the aerospace industry, this material is commonly employed in aircraft interior parts like seat frames and housings due to its flame retardancy properties.
Apart from its mechanical attributes, PA66 GF33 also offers good dimensional stability and low creep behavior under load. It has a high melting point which allows it to withstand elevated temperatures without undergoing deformation. Additionally, this material has excellent electrical insulation properties that make it suitable for electrical connectors and housings.
Overall, PA66 GF33 stands as a versatile thermoplastic that combines durability with enhanced mechanical properties for demanding applications in both the automotive and aerospace sectors. Its ability to withstand harsh conditions while providing lightweight solutions makes it an increasingly popular choice among manufacturers across various industries.
Automotive Applications:
PA66 GF33, also known as 33% glass fiber reinforced polyamide 66, is a high-performance thermoplastic material widely used in automotive applications. One of the key benefits of using PA66 GF33 in the automotive industry is its excellent mechanical properties, such as high stiffness and strength. This makes it an ideal choice for various components, including engine covers, intake manifolds, radiator end tanks, and air ducts.
Additionally, PA66 GF33 offers outstanding heat resistance and chemical resistance, making it suitable for under-the-hood applications where parts are exposed to extreme temperatures and harsh chemicals. The material also has low water absorption properties, ensuring dimensional stability even in humid environments. These characteristics make PA66 GF33 a reliable option for automotive manufacturers looking to enhance the durability and performance of their vehicles.
Moreover, the use of PA66 GF33 in automotive applications contributes to weight reduction efforts within the industry. As compared to traditional metal components, this lightweight material helps improve fuel efficiency while maintaining structural integrity. Furthermore, its ability to be easily molded into complex shapes allows for design flexibility and cost-effective production processes. With these advantages in mind, it is no surprise that PA66 GF33 continues to play a significant role in driving innovation within the automotive sector.
Aerospace Applications:
In recent years, the aerospace industry has witnessed significant advancements in the applications and innovations of PA66 GF33. PA66 GF33, a high-performance polymer composite material, has found extensive use in various aerospace components due to its exceptional mechanical properties and lightweight nature. One prominent application is in the manufacturing of aircraft structural parts, such as wing sections, fuselage panels, and landing gear components. The high strength-to-weight ratio of PA66 GF33 makes it an ideal choice for these critical components as it enhances overall aircraft performance while reducing fuel consumption.
Furthermore, PA66 GF33 has also been utilized in the construction of aerospace interior parts and systems. This includes seating structures, overhead bins, galley equipment, and lavatories. The excellent flame retardancy property of PA66 GF33 ensures enhanced safety measures by meeting strict aviation regulations regarding fire resistance requirements. Additionally, its superior dimensional stability allows for better fitting parts that can withstand extreme temperature changes experienced during aircraft operations.
The continuous advancements and growing applications of PA66 GF33 in the aerospace sector signify its remarkable potential to revolutionize the industry by offering improved performance characteristics while optimizing weight reduction efforts. With ongoing research and development initiatives focusing on enhancing its properties further, this high-performance polymer composite material is poised to play a vital role in shaping future aerospace designs and innovations.
Innovations in PA66 GF33:
The applications and innovations of PA66 GF33 are vast, ranging from the automotive industry to the aerospace sector. In the automotive field, PA66 GF33 is commonly used in various components such as engine covers, air intake manifolds, radiator end tanks, and fuel systems. Its high strength-to-weight ratio makes it an ideal choice for these applications, as it helps reduce overall vehicle weight while maintaining structural integrity.
In recent years, there have been several notable innovations in the use of PA66 GF33 in the aerospace industry. One such innovation is the development of lightweight composite materials for aircraft structures. By combining PA66 GF33 with other reinforcement fibers such as carbon or glass fibers, manufacturers have been able to create high-performance composites that offer significant weight savings without compromising on strength or durability.
Another area where there have been advancements in PA66 GF33 is in additive manufacturing or 3D printing technology. This innovative manufacturing method allows for complex geometries and designs that were previously difficult or impossible to achieve using traditional methods. By utilizing PA66 GF33 as a feedstock material for 3D printing processes, engineers can create prototypes and functional parts with enhanced mechanical properties and improved performance characteristics. Overall, the continued advancements and novel applications of PA66 GF33 make it a highly sought-after material across industries seeking lightweight yet strong solutions.
Advantages and Challenges of PA66 GF33:
PA66 GF33, also known as polyamide 66 glass fiber 33%, is a popular material choice in various industries. One of its key advantages is its high strength and stiffness, thanks to the addition of glass fibers. This makes it ideal for applications that require durability and structural integrity, such as automotive and aerospace components. Additionally, PA66 GF33 offers excellent resistance to heat and chemicals, allowing it to withstand harsh environments without compromising its performance.
Another advantage of PA66 GF33 is its ability to reduce weight while maintaining strength. The incorporation of glass fibers enhances the material’s rigidity without significantly increasing its density. This lightweight characteristic is particularly beneficial in industries where weight reduction plays a crucial role in achieving fuel efficiency or improving overall performance.
Challenges of PA66 GF33:
Despite its numerous advantages, there are certain challenges associated with the use of PA66 GF33. One main challenge lies in processing this material due to the presence of glass fibers. These fibers can cause issues such as wear on molds and machinery during manufacturing processes like injection molding.
Another challenge is related to cost considerations. The addition of glass fibers increases the production cost compared to standard PA66 resins. Therefore, manufacturers need to carefully evaluate whether the benefits offered by PA66 GF33 justify the additional expenses involved in using this reinforced plastic material.